FADEA y CONAE: Trayectorias que miran al espacio
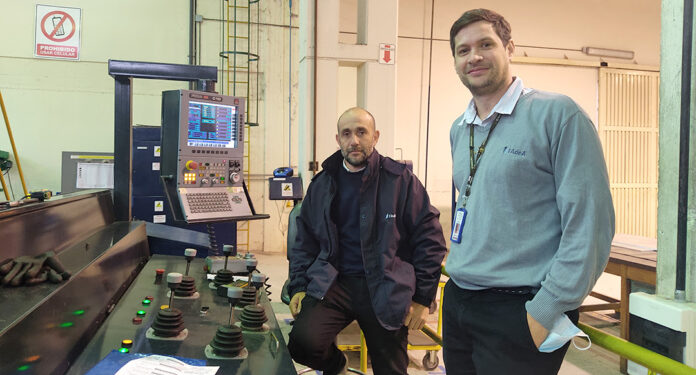
Tras décadas en las que la fábrica de aviones no participaba de la actividad espacial, la reciente producción de partes estructurales del nuevo tanque de combustible del futuro Tronador II marca un hito en la colaboración con VENG y la CONAE.
Agencia TSS – El 7 de julio pasado, en las instalaciones que la empresa VENG posee en Pipinas, en la provincia de Buenos Aires, una pequeña delegación de FADEA encabezada por su gerente general, Franco Giuggioloni, entregó los diez primeros gajos de lo que serán los nuevos tanques de combustible del futuro vector de acceso al espacio que está desarrollando la Comisión Nacional de Actividades Espaciales (CONAE), el Tronador II.
Hacía más de tres décadas que FADEA no se vinculaba a la actividad espacial nacional, algo que sorprende teniendo en cuenta el importante desarrollo que esta última ha tenido en la Argentina durante esos años, y el hecho de que la fábrica de aviones situada en Córdoba posee capacidades productivas que en muchos casos son únicas en el país y con potencial para la industria espacial.
La fabricación de los gajos de los tanques de combustible del Tronador II se enmarca en el proceso de desarrollo de este vector de dos etapas que, cuando esté finalizado y operativo (se calcula que para el año 2028) hará que la Argentina ingrese al selecto grupo de países con capacidades propias para poner artefactos en órbita. El Tronador II permitirá “inyectar” cargas útiles, como satélites, de hasta 500 kilos, en órbitas LEO (órbitas bajas de la Tierra por sus siglas en inglés) de unos 600 kilómetros de altura.
En el camino hasta llegar al lanzador definitivo hay una serie de pasos a seguir y de pruebas que realizar. Antes del modelo final, conocido también como Tronador 250 –por los 250 centímetros de diámetro de su fuselaje– se construirán dos modelos menores, el Tronador 70 y el 150 (70 y 150 centímetros de diámetro de fuselaje, respectivamente), que deberán estar listos para los años 2024 y 2026.
El programa de acceso al espacio de la CONAE se inició en el año 2008 con la serie de vehículos VEX y a la fecha debería estar mucho más avanzado, al igual que la construcción del sitio de lanzamiento ubicado en la Base Naval de Puerto Belgrano, al sur de la Provincia de Buenos Aires, pero durante el gobierno de Mauricio Macri el proyecto fue desfinanciado y paralizado, hasta que fue retomado en el año 2020.
Cuando se complete el programa del Tronador II, el proyecto habrá insumido un costo algo superior a los 400 millones de dólares, algo realmente económico dadas las cifras que suelen involucrar iniciativas similares en otras partes del mundo.
La empresa VENG es la proveedora principal de la CONAE en lo que hace al lanzador. Los modelos de evaluación tecnológica que se construirán (Tronador 70 y Tronador 150) constituyen lo que en la jerga interna de la empresa se denomina la “Serie Tronador” y su finalidad es ensayar sistemas específicos del cohete antes de fabricar y probar la versión final. Por ejemplo, el Tronador 70 servirá para probar la turbobomba y los motores de la segunda etapa; mientras que en el Tronador 150 se ensayarán los mismos subsistemas pero de la primer etapa.
El Tronador II estará equipado con tres motores de 30 toneladas de empuje cada uno, aunque se prevé una versión potenciada, denominada Tronador III, que portará cuatro de esos motores.
No ha sido sencillo el diseño y fabricación de los tanques de combustible. “Si bien es un lanzador, la ingeniería aeronáutica es clave para llegar al espacio. Poder tener una técnica que permita hacer los tanques de combustible del mismo espesor, en su estructura, que el fuselaje, es importantísimo por lo que significa en el ahorro de peso, cosa que no se estaba logrando haciéndolo con otras técnicas. También es importante que se haya podido hacer en el país, evitando mandarlo al extranjero, con ahorro de divisas; y además con otra empresa estatal, y que se empiece a colaborar entre las empresas estatales”, le dijo a TSS, Marcos Actis, presidente de VENG.
Gajos para un cohete
El Tronador II contará con dos tanques de combustible de oxígeno líquido y querosén por etapa. Cada uno de esos tanques es un cilindro de aluminio de ocho metros de largo por 2,5 metros de diámetro, cerrado en cada uno de sus extremos por una semiesfera compuesta por ocho gajos cada una de ellas. El desarrollo del proceso de fabricación de esos gajos fue lo que se le encomendó a FADEA. “En esta etapa, lo que nos han encargado es el desarrollo del proceso de fabricación de las piezas. El diseño es de VENG y nosotros hacemos un built to print, una fabricación bajo diseño, y somos los responsables del desarrollo del proceso de manufactura de las piezas”, le explicó a TSS Leonardo Carrizo, jefe del Programa de Aeroestructuras de FADEA, donde se lleva a cabo la producción de los gajos para el Tronador.
En el diseño del modo de fabricación de los gajos “se decidió usar el proceso conocido como stretchforming, conformado por estirado”, señaló Carrizo. “No sólo debimos desarrollar el proceso de fabricación –añadió–, sino también los moldes que iban a ser necesarios. Se contrató a una empresa especializada en este tipo de herramientas, Molaike, que está en Buenos Aires, y ellos diseñaron y fabricaron un utilaje de estirado y otro de contorneado. El primero se usa en la máquina Loire y el segundo para el mecanizado en una fresadora de cinco ejes FIDIA”.
Entre las máquinas-herramienta con las que cuenta FADEA, hay dos que se destacan: una es una máquina de estirado de 250 toneladas de presión marca Loire, y la otra es una fresadora a control numérico (CNC) de cinco ejes, marca FIDIA. Ambas están involucradas en la producción de los gajos para VENG.
La fabricación de cada gajo comienza tomando“la plancha de aluminio que se compra al proveedor de este material. Posteriormente, se corta la chapa de la forma definida por el área de Ingeniería de Proceso de FADEA, se le hacen distintos tratamientos térmicos para darle maleabilidad al material y, cuando está listo, se lo monta sobre el molde en la Loire y se comienza con varios ciclos de estirado”, relató Carrizo.
“Básicamente, agarramos la chapa en la máquina de estirado empleando dos mordazas y la estiramos arriba de un molde, logrando la forma que tiene éste. El proceso completo lleva varios estirados (cuatro) porque el material se va endureciendo, entonces se realizan recocidos previos a cada estirado, hasta que se llega a la forma final”, detalló a TSS Diego Maenza, líder de Ingeniería de Fabricación de los gajos.
El proceso de producción se diseña “primero en base a la experiencia que se tiene con piezas similares y luego se hace un try out (ensayo) con una pieza inicial y, posteriormente, con una segunda y una tercera, hasta lograr el proceso indicado. En este caso, lo conseguimos en la tercera pieza”, comentó Maenza.
El material empleado es una aleación de aluminio “AL 2219”, que viene en planchas de 144 por 48 pulgadas. El material fue provisto por VENG, que ya tenía en su stock las chapas, y para el futuro se está analizando usar una variante que emplea al cobre como aleación principal y es el mismo que usa FADEA en gran parte de los componentes aeronáuticos que fabrica. El problema de cambiar de tipo de aluminio es determinar si se comportará de manera similar, en cuanto a resistencia y maleabilidad, que la variante ya probada. Por otro lado, mudarse hacia un aluminio más disponible y que, a su vez, ya empleó FADEA, permitiría mejorar los tiempos y los costos de obtención del material. Frecuentemente, los productores internacionales de este tipo de insumos exigen compras por volúmenes mínimos y, cuando la cadencia productiva no es alta, ello puede implicar quedarse con stocks sin poder usarlos por mucho tiempo.
Después del estirado, las piezas pasan por un solubilizado al estado T42 (templado) y un calibrado en prensa. El templado permite obtener un nuevo nivel de dureza, pero el estado final del material se consigue luego de transcurrido 20 minutos desde que se realizó dicho tratamiento térmico, período en el que se debe dar a las piezas su forma final en la prensa.
“Lo que sale del estirado es un gajo de forma bruta –explicó Carrizo– al que falta darle todavía su configuración final, la forma que se necesita para que la pieza coincida con el utilaje de armado que tienen en VENG. Ese utilaje es de posicionamiento de los gajos y es donde luego se realizará la soldadura empleando el método de fricción, para lo cual disponen de una máquina especial”.
Una vez que se llega a la forma final, cuando la pieza ha copiado la forma del molde, se le hace un punzonado. “Es un agujero en la parte de la chapa que ha quedado por fuera de la pieza en sí y que sirve para ubicar la chapa en el utilaje de contorneado”, continuó Carrizo. Y Maenza añadió: “Después que se termina de estirar se va a un proceso de corte y luego a un envejecido artificial, que es un tratamiento térmico que le da aún mayor dureza a la pieza. Ese tratamiento tarda unas 36 horas en el horno”. El paso por la fresadora permite eliminar el material sobrante de la pieza y dejarla con su forma final.
Cada gajo pesa 30 kilos y tarda cerca de una semana y media en fabricarse. El lote piloto encargado a FADEA ha sido de diez unidades y, a partir de ahora, con el proceso productivo ya diseñado y probado, está previsto que VENG haga un pedido de 30 gajos más.
Cooperación intraestatal
Tanto FAdeA como VENG son empresas estatales. La primera es en un 99% propiedad del Ministerio de Defensa y el restante 1% de Fabricaciones Militares. La segunda es propiedad en forma mayoritaria de la CONAE, con un pequeño porcentaje en manos de INVAP y de Servicios Tecnológicos Integrales (STI).
“En el año 2012, desde otra posición en la universidad [Nacional de La Plata], había hecho una visita a la fábrica y había visto que se podían estirar las chapas y hacerlas tomar distintas formas. Así que ver hoy concretado que FADEA, luego de varias idas y vueltas, haya podido hacer los gajos, es una alegría y reconforta”, señalóActis.
El presidente de VENG enfatiza lo virtuoso que resulta la colaboración entre las empresas estatales. “Tienen que complementarse y ser competitivas en lo que le toca a cada una”, dijo Actis. Y agregó: “Me parece que lo mejor es aprovechar las capacidades y, aunque los gajos parezcan una cosa chica, es un camino que se inicia. VENG tiene que crecer en lo que es fuerte, como la soldadura por fricción, y aprovechar las capacidades de otras empresas. Inicialmente se tuvo una idea, con la que uno no estuvo de acuerdo, que es querer hacer todo, y eso ya no se usa. VENG en Pipinas debería funcionar en la parte de la construcción y ensamblado del lanzador, y a lo sumo tener lo relativo a la soldadura por fricción y la fabricación de componentes menores. Incluso partes como el fuselaje o los tanques podrían viajar a Córdoba para los ajustes y luego volver a Pipinas para el ensamblado final”, detalló Actis.
“Hay que optimizar los recursos y no duplicarlos. Lo mismo con los privados. Si hay una empresa privada que pueda hacer determinadas piezas, es preferible apelar a eso y no tener un equipamiento para hacer una pieza cada tanto”, continuó el presidente de VENG.
Los lanzamientos de prueba de la “Serie Tronador” se realizarán desde las instalaciones que CONAE posee en Pipinas, mientras se avanza con las obras de Puerto Belgrano.
Originalmente, también se había previsto en el proyecto que el querosén se produjera en la Argentina a través de YPF, pero la planta que se iba a montar en La Plata por ahora no ha comenzado su construcción. De todas maneras, la cooperación entre empresas estatales y con privados está permitiendo avanzar en la nacionalización de porcentajes importantes de las partes y los procesos productivos del futuro Tronador II.
Diego Maenza (izquierda) y Leonardo Carrizo en el tablero de control de la Loire, una de las máquinas de conformado por estirado de FAdeA.
Fuente: unsam.edu.ar